Radial Benders
DCME
- Minimal feeding time, allowing bending operations to
be executed at maximum speed. - Bending angle to be set up to 360°
- Press cutting speed and positions to be optimized, thereby increasing feasibility of parts (for example to let a deep punching go through the tooling) and
sharpening frequency to be reduced. - Tools to remain under constant monitoring ; the system checks at all times the power consumption of each motor, compares the data to minimum and maximum values for the part produced and stops the machine if any data go out of tolerances.
- Mechanical chain to be simplified, brings ease of maintenance and lowered frequency and costs.
Bending units
Tables have two working sides, connected through their centers. “Table + tooling” are interchangeable sets, allowing a quick production change-over. They are movable from left to right, allowing to precisely center the press efforts, regardless of the developed material length.
Slides and drive shafts take their movements at any position on the main gear. They can be freely positioned depending on the desired working angle.
The back table is fitted with 8 equidistant power takeoffs, for the driving of slides and additional movements.
Generally equipped with an “extraction system”, through a double positive movement, it ensures safe parts ejection.
Slides, using double positive cams, and other elements mounted on the tables are removed and repositioned in a few minutes.
Feeding systems
By means of double-clamping jaws or quick-opening rollers, with controlled opening, material can be fed
from several directions, namely from left, right, front and back.
Presses
Of “swan neck” type. Their one-piece sturdy sides allow to avoid the use of front rods. Press-tables are generously sized.
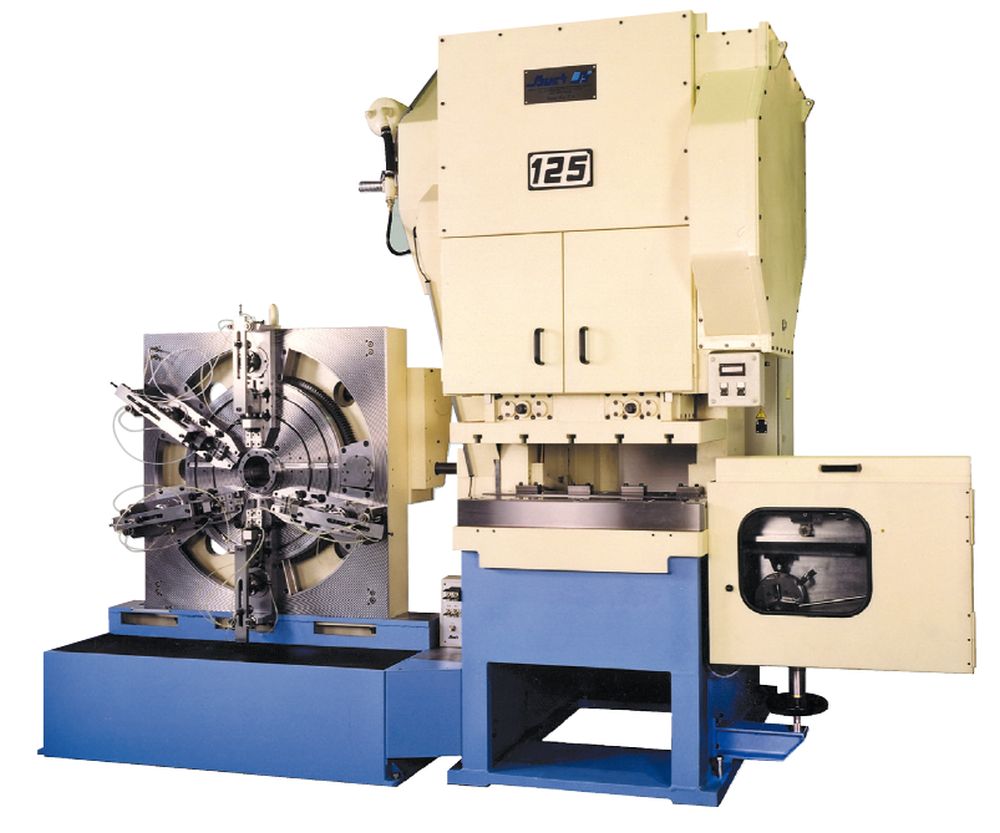
Technical characteristics
Model | Production rate (ppm) |
Press (t) |
Maximum wire feed (mm) |
Material (mm) | |
Maximum wire diameter (mm) |
Max. strip width (mm) |
||||
DCME-100 S | 0 – 1000 | 100 | 2 | 20 | |
DCME-100 P-5 | 0 – 1000 | 5 | |||
DCME-200 S | 0 – 400 | 200 | 4 | 40 | |
DCME-200 P-10 | 0 – 400 | 10 | |||
DCME-200 P-15 | 0 – 300 | 15 | |||
DCME-200 P-25 | 0 – 200 | 25 | |||
DCME-300 S | 0 – 150 | 300 | 4 | – | |
DCME-400 S | 0 – 180 | 400 | 8 | 60 | |
DCME-400 P-25 | 0 – 180 | 25 | |||
DCME-400 P-60 | 0 – 140 | 60 | |||
DCME-400 P-80 | 0 – 140 | 80 | |||
DCME-400 P-125 | 0 – 80 | 125 | |||
DCME-450 S | 0 – 180 | 450 | 8 | 140 | |
DCME-450 P-60 | 0 – 140 | 60 | |||
DCME-450 P-80 | 0 – 140 | 80 | |||
DCME-450 P-125 | 0 – 80 | 125 |
Videos
Pictures
25 t press
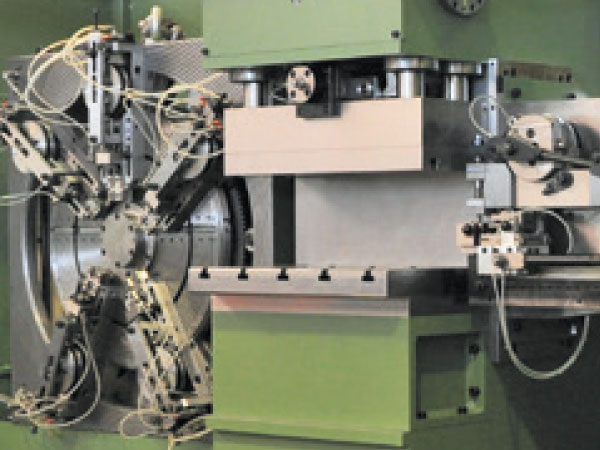
Back movement
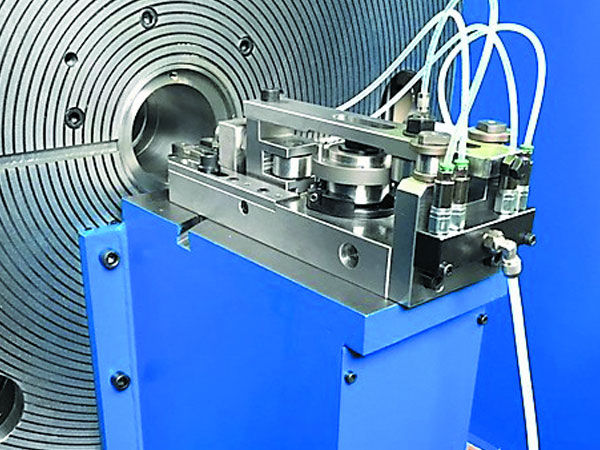
Roller feeding
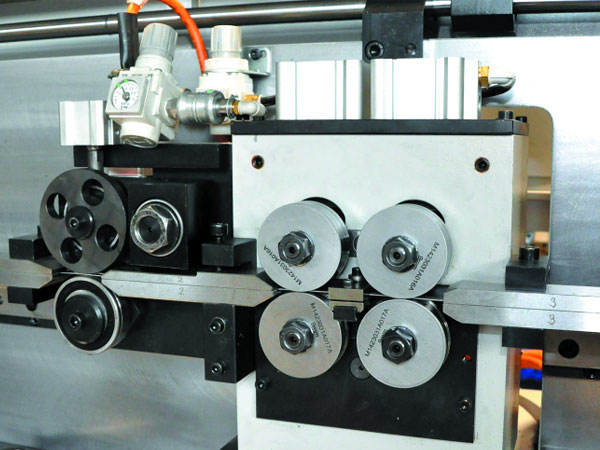
Back movement with torsion spindle
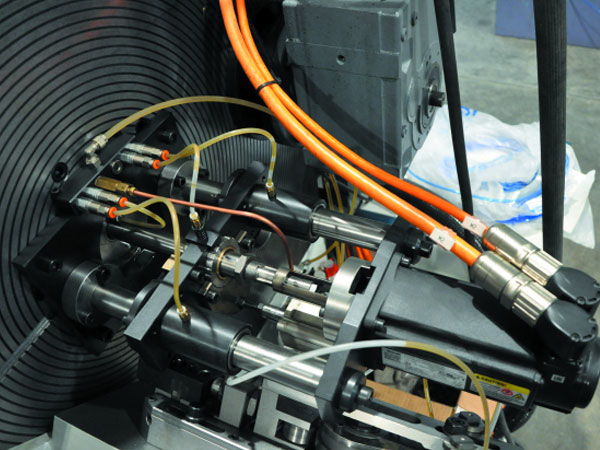